PRINTING OPERATIONS: SURVIVE TO THRIVE - AN INTRODUCTION TO 5S by Andrew Malson
Introduction
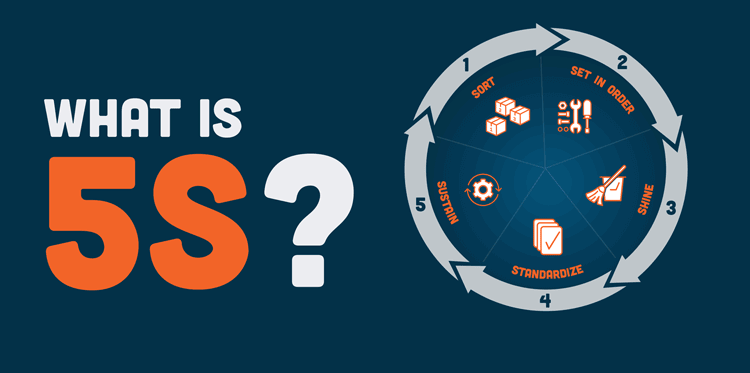
(c) graphicproduct.com
Over my many years of 5S implementation in print companies, I have come across several epithets attributed to the system but this struck me as the most appropriate for this era:
The comprehensive implementation of each S is the starting point in the development of improvement activities that enables any company to survive.
Every manufacturing company needs to understand waste and create value in their working practices and 5S is the systematic method for doing so. In these series of articles, I hope to explain the concept of the 5S system and why it will help print businesses reach far beyond survival in the COVID era.
The S’s – where and why
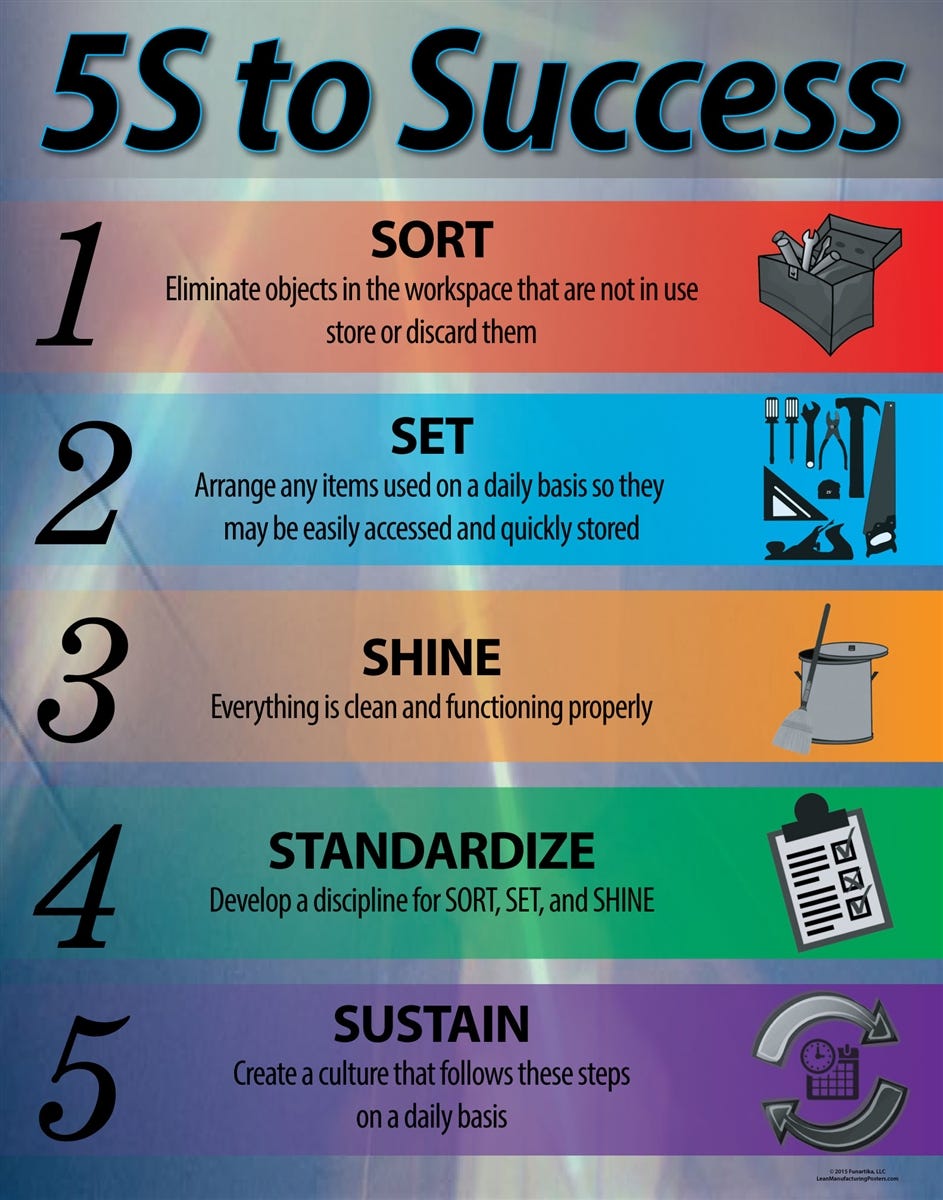
(c) graphicproduct.com
5S was conceived in post WWII Japan, as a part of what became known as the Just In Time (JIT) manufacturing system.
Sakichi Toyoda, the founder of the Toyota motor company, employed the moving assembly process but recognised that waste existed in the process. As the need for higher output increased, so did the impact of waste and Toyoda created what became the forerunner of 5S and Lean methodologies.
I work in a print company, what’s 5S got to do with me?
I hear the above argument in many print businesses. Printing is manufacturing and manufacturers the world-over have the same issues and problems. If you produce non-conforming product, if your deliveries are not on time, if your printing output is low; all these issues are manufacturing issues that will be addressed through a 5S programme. Add to that a marked improvement in safety, which in turn leads to an uplift in employee morale and 5S becomes the reason for improvement and improvement enables a business to thrive beyond survival.
Some examples:
· Wrong ink, plates or paper/board. Incorrect decisions made by operators acting on “initiative”, missing or mislabelled information and mixed Work-in-Progress. All are causes of non-conforming product.
· All of the above plus lack of supply to the press for ink/plates/blankets etc will cause delays in delivery and also low output.
· A disorganised pressroom is unsafe. If people feel safe within their environment, they will work better and more efficiently.
IMPLEMENTING THE PROGRAMME
Start simple. With any new management system, communication and education is necessary, and 5S is no exception. As a matter of fact, 5S might be such a paradigm change to the business that clear communication is vital for a successful implementation.
Communicate, what 5S is, how it will be implemented and why the business is implementing 5S. Fundamentally, people need to understand, before they “buy in” to any new change, so ensure that the benefits are properly accentuated (the What’s In It For Me factor).
Choose a pilot. 5S should be applied across the whole business but it can easily become unwieldy. Choose a specific area of the factory that will most benefit from the improvements and is also visible. When choosing the location, consider the people within that area; the pilot will work best where the people are enthusiastic and open to 5S.
The steps
Below is a picture of a printing press, take a look at the press and the surrounding area and think about how to apply the 5S system:
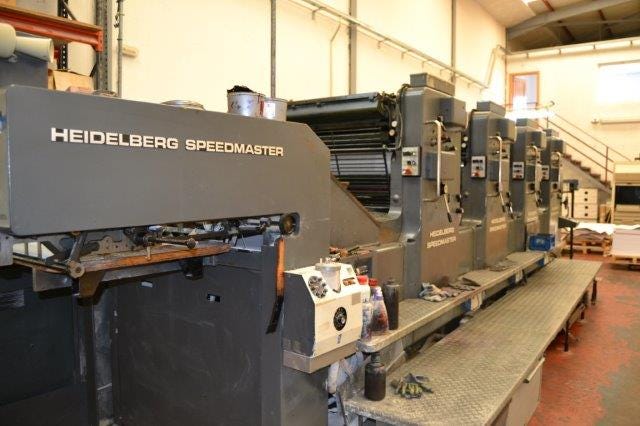
The first, important, step is to take a picture, as above, to show the machine and the area in its present condition, this will be used for the before and after picture.
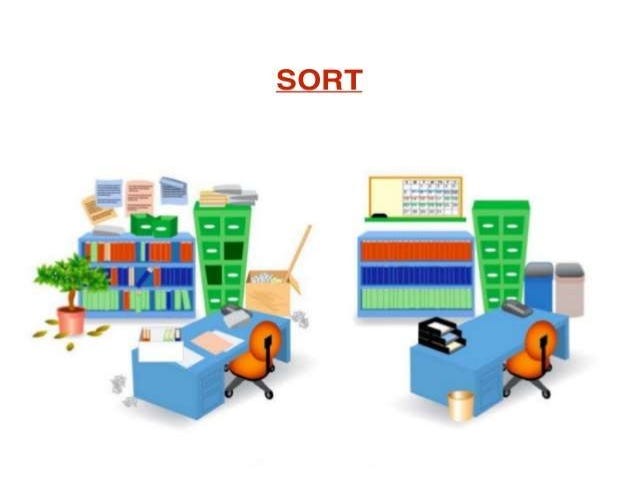
(c) Slideshare
By applying the first S, Sort, we would be looking to identify what is needed. We seriously need to “declutter” the area before we move further; gloves, various chemicals, rags tools etc, none of that needs to be on the press to operate it, so identify it to move later, or move it immediately (here the ink is needed but is in the wrong place). Consider pallet locations and moving equipment. Labelling also comes into play here, if one needs to ask, “what’s that for?” - it needs identifying.
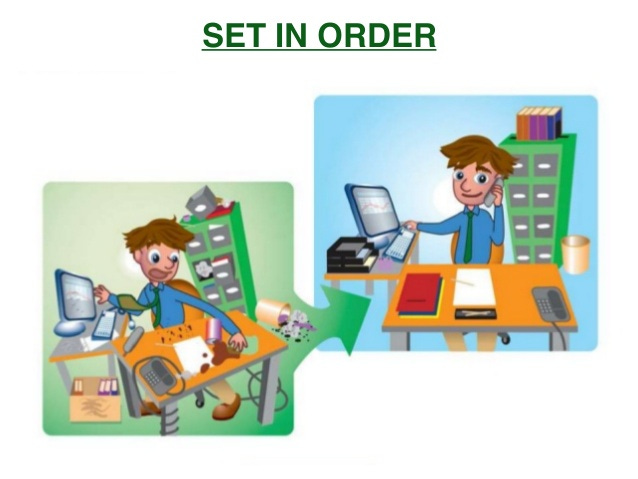
(c) Slideshare
Set involves placing the items required in the most appropriate location, dependent on frequency of use (see ink – above). Tools are often an offender here, with some being put into the recesses of the press or on top of the print units (a particular annoyance of mine). Not only is there the potential for loss of the tools or serious damage to the machine but tools used a few times day shouldn’t, in any case, be left on the press. The general rule for tools is frequency = proximity; if you use a tool constantly, keep it close (a toolbelt, for example), for tools used less frequently, store them away from the equipment.
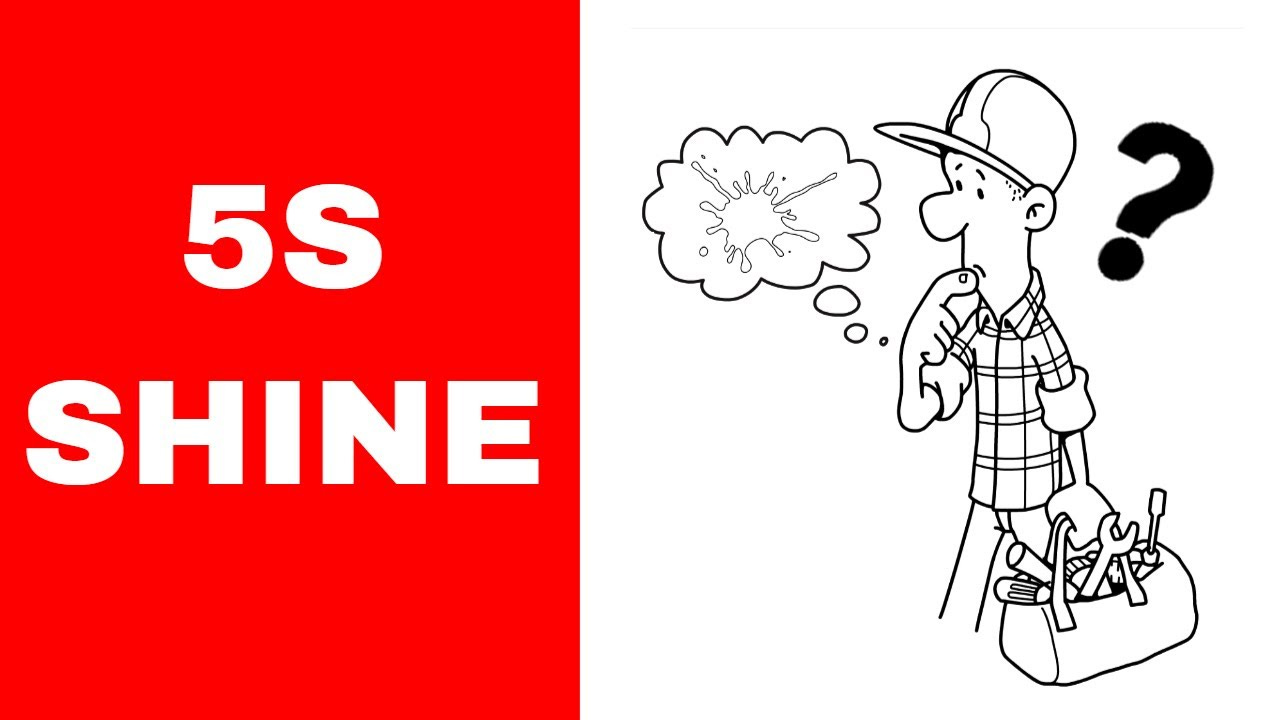
(c) LeanVlog
Shine is quite self-explanatory, but is it? A superficial clean of the outside of the press and the surrounding area might last beyond the next manager’s inspection but it doesn’t add any value to the printer. Keeping the area and the press clean should translate as maintained and productive. Dirt and detritus, if left to accumulate, will create issues with product quality.
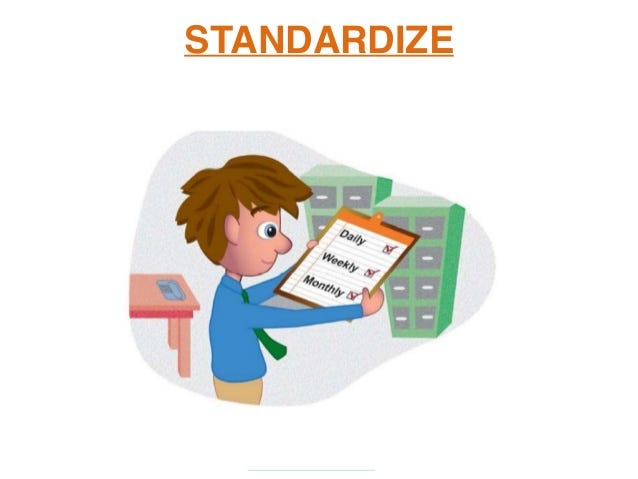
(c) Slideshare
Standardise is all about locking down what we’ve already done; although the system, when maintained properly, will identify various changes and improvements, as it becomes more mature. Standardising supports what has gone before.
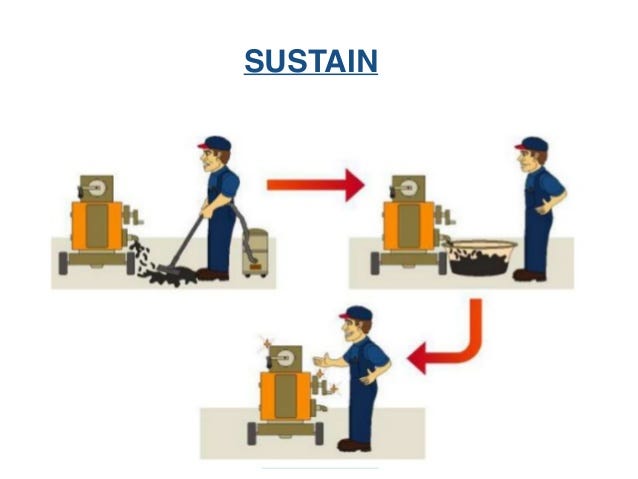
(c) Slideshare
If I said that I’ve seen a print business that has reached the 5th S, Sustain, then I wouldn’t be being entirely honest. I’ve been there at the start of many 5S programmes and, while I’ve seen some rapid and exemplary implementations, the systems have needed time to grow. 5S hasn’t reached the 5th level because it is changing; maturity of the system will create Sustain, which in turn results in efficient, value driven manufacturing.
Conclusion
5S has been around since the middle of the last century, yet the print industry, certainly across Europe and North America, seems reluctant to embrace it. Given the times that we are in, only print businesses that address non-conformity, lack of output and inefficient practices will survive and thrive.
This is an introduction to the concept of 5S, future articles will look at 5S and its associated tools in more detail.
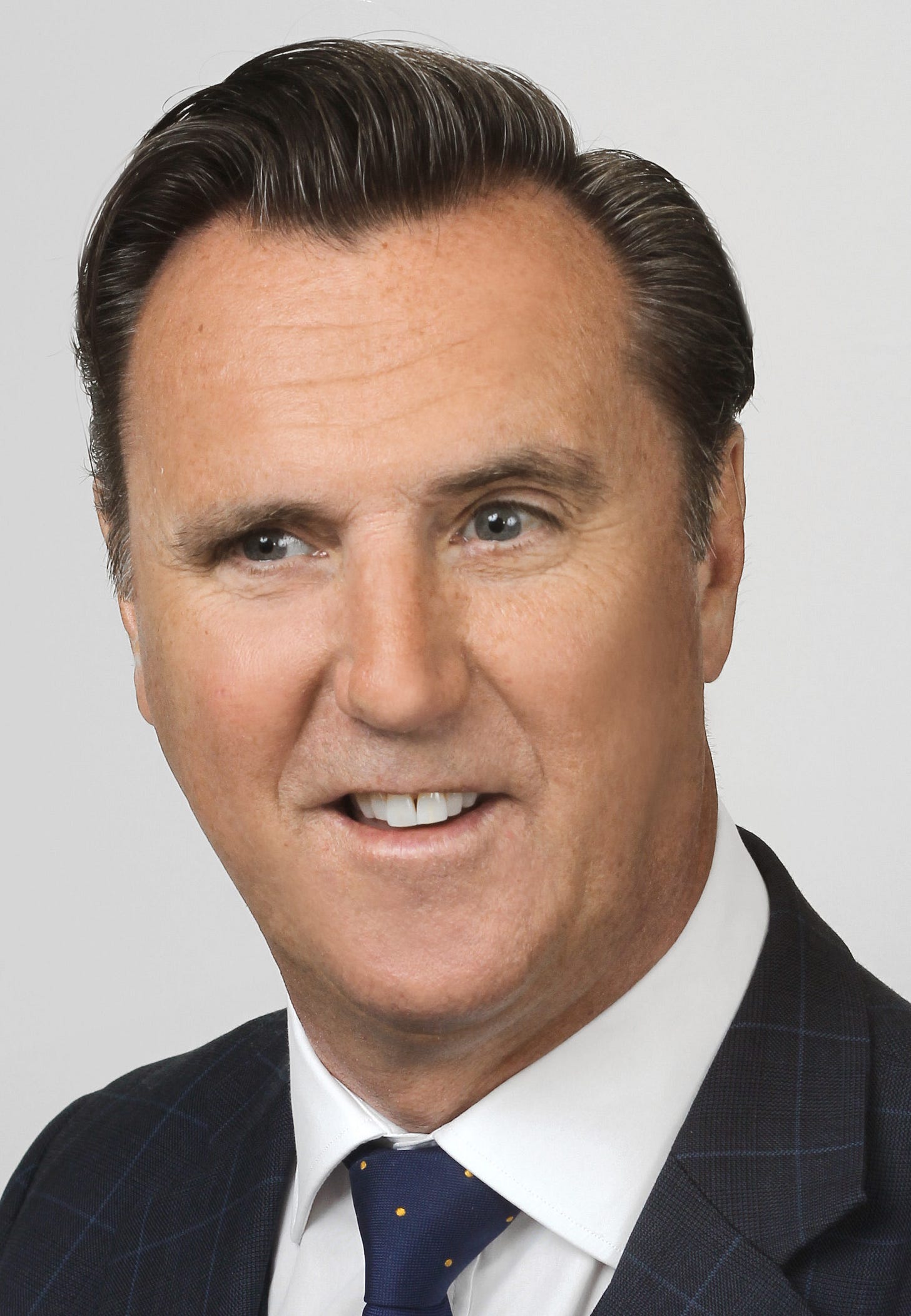
Andrew Malson is a highly experienced, committed and passionate Operations Executive/Director/Manager with a demonstrable reputation for creating the change required to deliver significant improvements in business performance through quality, service and productivity. He has invaluable strength in establishing and ensuring sustainable success of single, multi, and regional manufacturing sites by creating right and enduring cultural change through involvement and development of people. In the 30 years since beginning in the industry, Andrew has been responsible for the design and implementation of systems covering quality, people development, environmental standards and operational excellence. He brought his wealth of experience and invaluable knowledge to bear at WHERE To Print magazine in West Africa in its quest to positively influence and improve print purchase decisions with special focus on Lean Manufacturing Implementation; Organisational Effectiveness; and Sustainable Business Growth. Andrew welcomes your connection via wheretoprint@yahoo.com or directly vide andrewcmalson@gmail.com
NB: Information on joju.substack.com is mostly adapted or culled from press releases or supporting affiliates’ contents and are thus copyright materials. These are not in any way the personal thought, opinion or view of the Publisher.