AGFA INNOVATIONS THAT SUPPORT PRINTING COMPANIES
Since hosting its six-day live virtual event - Studio 4D48 last month, print technology giant - Agfa-Gevaert (Agfa) launched series of innovative technologies to support printing companies worldwide through the current business challenges and help them plan for the future.
Check out some of Agfa’s latest made-to-measure printing innovations which include printing plates, hardware and a range of workflow, colour management, print standardization and screening software that are expected to make print operations more economical, ecological and extra convenient. This is in addition to expanding its inkjet ink production capacity to meet growing demands.
AGFA’S ADAMAS CHEM-FREE PRINTING PLATE DELIVERS ENHANCED PERFORMANCE AND ECO-FRIENDLINESS

The latest version of Agfa’s Adamas chemistry-free offset printing plate boasts increased eco credits, in addition to extended run lengths for UV ink printing.
The combination of eco-friendliness with high press performance, sharp dot reproduction and maximum throughput, makes Adamas an ideal fit for both packaging and commercial (sheetfed or non-baked heatset) printing. The new generation comes with a number of ecological improvements, as well as increased performance in UV printing.
Durable print performance
Printing with harsh UV inks or opaque white ink can be quite exacting, but the latest version of Adamas achieves stable printing results and run lengths up to 75,000 when printing with UV inks – including conventional UV as well as H‑UV/LED-UV inks. With oxidative inks, run lengths amount to 350,000 copies.
The next level in eco-friendliness
The combination of the Adamas plate and clean-out unit completely eliminates the need for rinse water, and replaces chemicals with a pH neutral gumming solution. In the new version, the replenishment rate of the latter has been further reduced. All of this results in a waste decrease by up to 75% compared to similar products, less disposal costs and a safer work environment.
The second generation of the plate extends bath life to 8,000 m² of printing plates, which means that a printer with an annual plate consumption around 30,000 m² will only need to change the bath four times per year.
The range of Adamas clean-out units, which is based on Agfa’s patented cascade system, is extended with the new Adamas COU150, which can handle plates up to 1480 mm wide. “Adamas is truly unique in its class because it combines outstanding press performance with a minimal ecological footprint. It is the most durable chem-free plate system available on the market,” says Iris Bogunovic, Product Manager Plate & CTP Systems. “The latest generation offers printers even more value for their business.”

KLS PurePrint is one of Denmark’s largest printing companies. It aims to live up to the highest environmental standards and continuously raises the bar regarding sustainable print production, which is also what their customers expect. They were the second company worldwide to obtain ‘Cradle-to-Cradle’ certification. Agfa’s Adamas plates and COU perfectly fit in their sustainability strategy. “Our sustainable strategy will continue to be our primarily focus. However, our customers also expect products that meet the highest quality standards, on-time deliveries, and competitive pricing,” says CEO Kasper Larsen. “We see Agfa as an important strategic partner as they maintain a high production standard, and we expect them to continuously focus on developing the most environmentally friendly prepress solutions.”
“Since we switched to Adamas, we can handle longer print runs,” adds Prepress Manager Keld Kortbæk. “Futhermore, the plate’s excellent image contrast enables an easy visual check to avoid any mistakes. Scratch resistance is great too.”
ECO³ innovation
Adamas is a prime example of Agfa’s ECO³ approach, consisting of a wide range of hardware, software, consumables and services that make printing operations cleaner, more cost-effective and easier to manage and maintain.
NEW ATTIRO CLEANING MODULE REDUCES MAINTENANCE IN PREPRESS
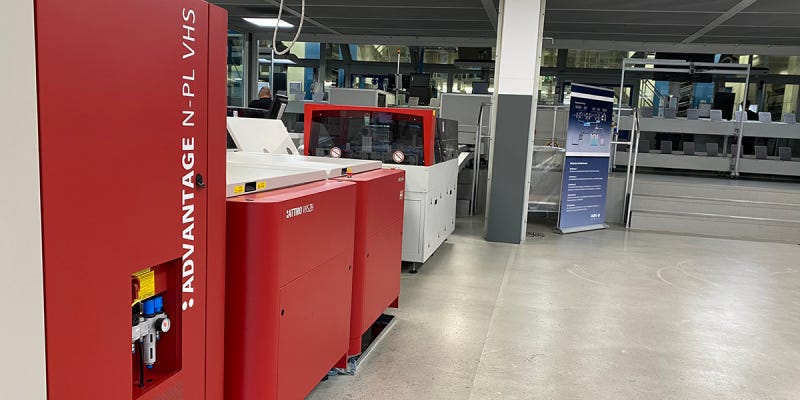
Added to Agfa’s Attiro clean-out unit for violet newspaper printing plates is a cleaning module to significantly reduce maintenance frequency of the Clean Out Unit.
The Attiro Cleaning Module gives newspaper printing companies the freedom to clean their Attiro clean-out unit after 12,000 m² of printing plates only. This reduces the workload for most users to three or maximum four full cleaning interventions per year. The Attiro Cleaning Module adds to the ease of use of Agfa’s violet plate technology Avatar V-ZH and N95-VCF in combination with the company’s Attiro clean-out units.
“Prepress staff of newspaper printers worldwide highly appreciated Agfa’s Attiro cascade clean-out unit, which is characterized by a minimal use of clean-out fluid, easy maintenance, and limited energy consumption,” says Rainer Kirschke, Market Manager Newspapers for Agfa. “In addition, the system’s small footprint makes it possible to move plate production closer to the press console for higher efficiency. In line with our ECO³ strategy, the new Attiro Cleaning Module makes this plate production solution even more ecological, economical and convenient.”
The Attiro Cleaning Module can be implemented in all existing Attiro units and is available to all Agfa plate users.
NEW ROBOTIC PLATE LOADER BOOSTS AUTOMATION AND PRODUCTIVITY
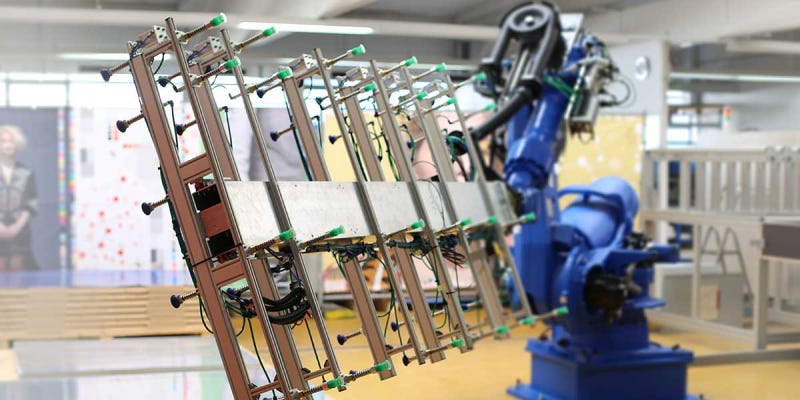
Agfa introduces a plate loading robot that streamlines and speeds up printers’ prepress operations, while reducing the overall cost.
Agfa’s robotic plate loader frees prepress staff from heavy manual, repetitive tasks such as plate loading cassettes of autoloaders, or fixing pallets on the base frame of skid loaders. “Heatset printers usually have multiple presses with different sizes, and therefore multiple CTP lines. Linked to that come so-called COMBO loading configurations, each consisting of a pallet loader and autoloader. The robotic plate loader replaces both configurations, reducing footprint by up to 30%, and making prepress operations more efficient and productive,” says Iris Bogunovic, Product Manager Plate & CTP Systems at Agfa.
In a first phase, Agfa offers its plate loading robot to printing companies using its Avalon VLF platesetters. The robot is custom-built according to a printer’s exact needs and can simultaneously feed multiple plate production lines with a picking speed of up to 80 printing plates per hour, independent of plate size. The set-up is especially convenient for printers that need to handle multiple (up to five) plate sizes. For optimal ease of use, the plate loading robot is fully integrated with Agfa’s Apogee workflow software.
Leading Scandinavian printed marketing solutions provider Stibo Complete is an early adopter of Agfa’s robotic plate loader. As the company’s strategy for the future includes a whole range of investments, as well as acquisitions of companies, one of the conditions for its success is the configuration of its print business to handle more output with less resources. The investment in Agfa’s new state-of-the-art plate loading robot supports their journey perfectly. “Automation is important in the strategy of any growing and forward-looking company,” says Svend Erik Grue Nielsen, Operations and Development Manager at Stibo Complete. “Agfa’s robot plate loader gives us a competitive edge as it improves our productivity, reduces costs, minimizes mistakes and optimizes working conditions for our employees. Our plate loading robot saves employees from approximately 230 tonnes of heavy lifting per year.”
NEW VERSION OF ARKITEX PRODUCTION WORKFLOW SOFTWARE FOR NEWSPAPER PRINTERS
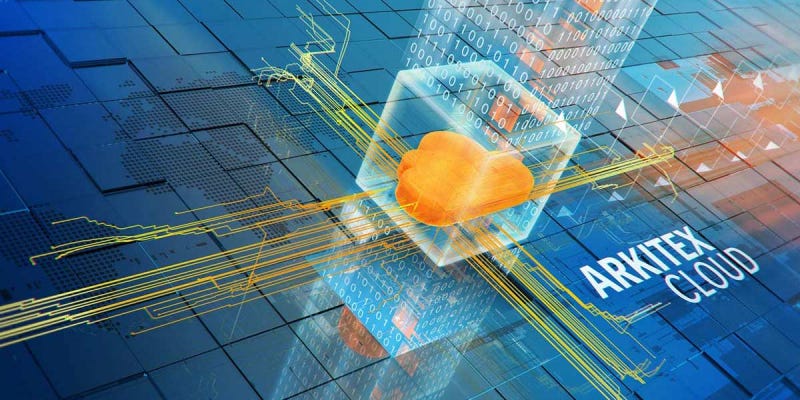
Arkitex Production v4.0 takes the next step in streamlining and automating newspaper print production workflows to save newspaper printers time and money.
This latest version focuses on a tighter integration with press management systems for just-in-time plate delivery, and incorporates multi-tenant capabilities as well as improved planning and tracking. Deployment in the cloud guarantees smooth business continuity.
Multi-tenant capabilities
Arkitex Production 4.0 supports multiple tenants on a single server, enabling them to access and benefit from the same software modules (such as RIPs, imposition, ink presets, etc.). Each tenant has its own users and permissions, plate layouts, products, and can only see their publications and templates. This becomes important in view of both local centralization and cloud workflow solutions where multiple sites can share hardware and resources while maintaining data security and workflow control.
Just-in-time plate delivery
Arkitex Production 4.0 can be integrated more tightly with printer’s press management and plate stacking systems, enabling a just-in-time delivery of plates to press. This way, plates can be produced in a shorter timeframe and arrive at the right moment at the right press tower.
The press operator – who in many cases is responsible for both prepress and press – can manage the entire workflow from one place. This includes automatic optional release of plates as soon as stacker bins for the next press run become available. This increases press efficiency and reduces press idle time.
At Media group MainPost (Würzburg, Germany), the purchase of new presses put new requirements to their plate workflow process. The company connected not only its platesetter from Agfa, but also its punch & benders, and its plate sorting unit to Arkitex and moved all of them close to the press console. “Plates are delivered just in time to the press towers now. This saves us time and costs, while production stability has increased”, says Thomas Gabel, production manager from the Mainpost site in Würzburg, Germany. “With this investment, we are prepared for the future.”
Improved planning, tracking and fan-out compensation
The updated Arkitex Production GUI contains many improvements in planning, status communication, and workflow tracking. With a single mouse click the new Edition Planning Wizard now enables operators to use an existing product template to instantly create a new edition plan. Plan automation can automatically create a template-based plan a defined number of days before production. These templates differ by day of week and, once a plan is created, users can modify the specific plan to adjust for specific differences.
In addition, production monitoring and tracking functionality from a single view has been enhanced. New visual indicators notify an operator of an action that may need to be taken, such as a plate approval. The ability to easily filter various queues by criteria such as page count, page version, job status or time range is another benefit allowing users to more easily focus on critical work. And to accommodate for web growth, the fan-out functionality that shifts and scales separations per press position also got an upgrade allowing for more precise image adjustment.
Cloud-based for guaranteed business continuity
Arkitex Production is available both on premise and as cloud-based solution. “Cloud-based services offer huge benefits,” says Jeff Cord, Product Manager Newspaper Software. “Newspaper printers do not need to spend time or money on IT infrastructure, server maintenance, or software updates. Systems are monitored and optimized 24/7 by experienced IT people and Agfa newspaper workflow experts. Uniform and standardized operations lead to better print quality, higher process efficiency with less downtime, guaranteed system stability and business continuity. By the way, Agfa’s cloud infrastructure is also used to host all of our hospital software solutions worldwide.”
Dedicated to newspaper printing
“More than ever, a streamlined, reliable and automated workflow is absolutely crucial for newspaper print sites to deal with the daily challenges and keep their competitive position,” says Rainer Kirschke, Market Manager Newspapers at Agfa. “We are committed to supporting the newspaper printing industry. Arkitex Production v4.0 contains numerous features that will increase operational efficiency and reduce costs.”
AGFA’S NEW PRINTSPHERE DISASTER RECOVERY
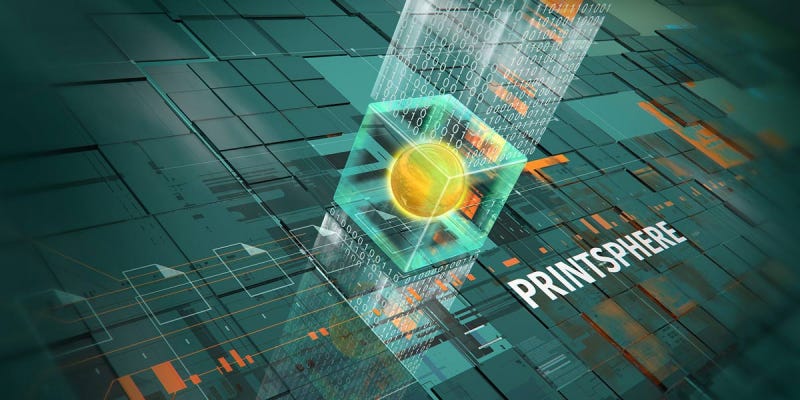
PrintSphere Disaster Recovery is a new module that provides newspaper printers with a secure backup that guarantees their newspapers will get printed in any event.
PrintSphere is a cloud-based, SaaS solution for standardized and efficient data exchange and workflow automation. Hosted by Agfa’s private and secure cloud, it makes it easy for printers to store data online and swiftly exchange files with any stakeholder.
Using the PrintSphere Disaster Recovery module, Arkitex workflow software users store all incoming publishing files in Agfa’s secure cloud in an automated way. In case of an emergency, a print partner or backup print site can get easy and fast access to the stored data and resume printing. This gives newspaper printers the guarantee that their daily newspaper will get printed – even if the press or the entire production site is down. PrintSphere Disaster Recovery also resolves potential issues with FTP transfer, including transfer speed, and provides a more secure and reliable platform.
AGFA INCREASES INKJET INK PRODUCTION CAPACITY
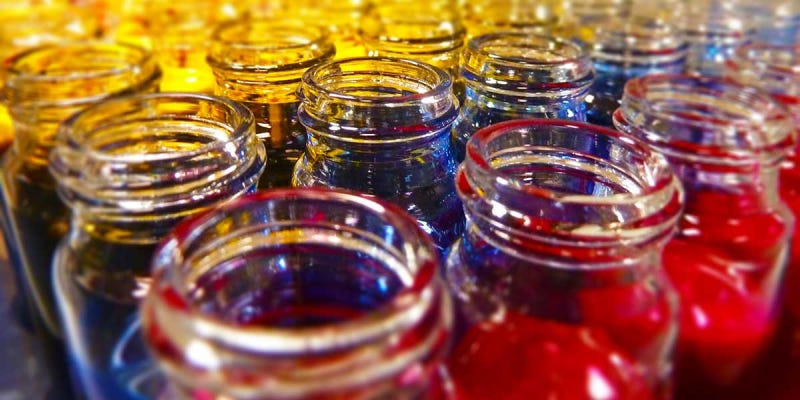
In a related development, Agfa will significantly invest in the expansion of its inkjet ink production capacity in order to cope with growing volume demands.
The new production facility – located at Agfa’s headquarters in Mortsel, Belgium – will enable Agfa to serve its current customers, as well as to be a key supplier of aqueous inkjet inks for a wide range of novel applications. Its first target is the growing market of printing on décor paper for the production of laminate floorings and furniture panels, where inkjet printing with Agfa’s water-based inks delivers a very cost-effective solution. The second target is the promising market of inkjet printing on packaging, especially on corrugated carton, delivering the most sustainable solution in terms of the material, as well as the printing process and ink.
In combination with Agfa’s existing facilities, the new plant will form a flexible and extremely efficient production centre, where R&D and Quality Control teams will be co-located. Its manufacturing capacity should cover the expected growth rates of ink volumes for the next five to ten years. “Agfa is a specialist producer of inkjet inks and fluids of renowned quality and performance. The inkjet ink business is one of our growth pillars,” says Tom Cloots, Director Industrial Inkjet. “In the last two decades, we built an inkjet ink production platform which covers pilot to full-scale ink production, and incorporates pigment dispersion production, extensive quality control and ink consistency programs. Our ink sales volumes have steadily grown year after year and we have gradually increased production capacity. The time has come for a new investment to keep up with growing market demands.”
UV-curable inks
Agfa is well known for its portfolio of high-performing wide-format UV inkjet printers, including the Anapurna and Jeti printer families, and the company’s latest addition, the Oberon. Powered by in-house developed and manufactured inks, these printers combine extreme productivity with extreme quality. The ink formulations are perfectly matched with the printer components (print head, curing, etc.), as well as with colour management software and print conditions (e.g. number of print passes) in order to deliver the lowest ink consumption and thus the lowest running cost.
In addition, Agfa develops and manufactures UV ink sets in close collaboration with a high number of Original Equipment Manufacturers (OEMs) of multi-pass and single pass printing solutions. Not only do these inks deliver high print quality and day-to-day reliable print results, but they also stand out through their wide colour gamut, excellent jetting reliability, superior shelf life and outstanding batch-to-batch consistency.
Water-based inks
For many years, Agfa has also been active in the field of aqueous inkjet inks, which are based on specific pigment dispersion and ink technology. OEMs incorporate these ink sets in their inkjet printing systems for diverse applications, including laminate (flooring and furniture, printing on décor paper), corrugated carton and document printing, as well as for ongoing developments, especially packaging applications. The ink sets are tuned to the print system as well as to particular application needs. The primary focus lies on printer uptime and the highest consistency of print results – day by day, week by week, month by month.
NB: Information on joju.substack.com is mostly adapted or culled from press releases or supporting affiliates’ contents and are thus copyright materials. These are not in any way the personal thought, opinion or view of the Publisher.